Gaskets create a positive seal between stationary parts. Gaskets must create an initial seal and then maintain that seal over a length of time. When useful life is finished, a gasket should be easily removable in order to be replaced.
Factors Influencing Gasket Performance
External factors change gasket and seal effectiveness
- Must seal system fluid.
- Chemically resists system fluid to prevent serious impairment of its physical properties.
- Deforms enough to flow into the imperfections on the gasket seating surfaces to provide intimate contact between the gasket and the sealing surfaces.
- Withstands system temperatures without serious impairment to performance properties.
- Is resilient and creep resistant enough to maintain an adequate portion of the applied load.
- Has sufficient strength to resist crushing under the applied load, and maintain its integrity when being handled and installed.
- Does not contaminate the system fluid.
- Does not promote corrosion of the gasket sealing surfaces.
- Is easily and cleanly removable at replacement.
During the gasket product selection process, Sealing Devices recommends that these factors be used as a checklist to determine optimal seal performance for your application.
Here are some critical items to consider when choosing gasket materials, including correct bolting pattern recommendations for common configurations.
There are also size, temperature, application, media, and pressure (STAMPS) guidelines for improving gasket sealing performance. Use correct bolt-torque, and re-torque within 24 hours.
S.T.A.M.P.S. for Selecting the Right Gasketing
Listed below is the information required to properly select the correct gasketing for your application.
Size: |
Normal pipe size and flange class – It non-standard size, you need: • ID and OD • Material thickness • Bolting dimensions |
Temperature: |
Of product being sealed • Continuous operating temperature • Maximum temperature |
Application: |
Type of equipment • Flange gasket? Pump casing? Heat exchanger? Bolt grade? |
Media: |
What material is to be sealed • Caustic? Steam? Acid? |
Pressure: |
Internal or system pressure • Operating pressure • Maximum pressure |
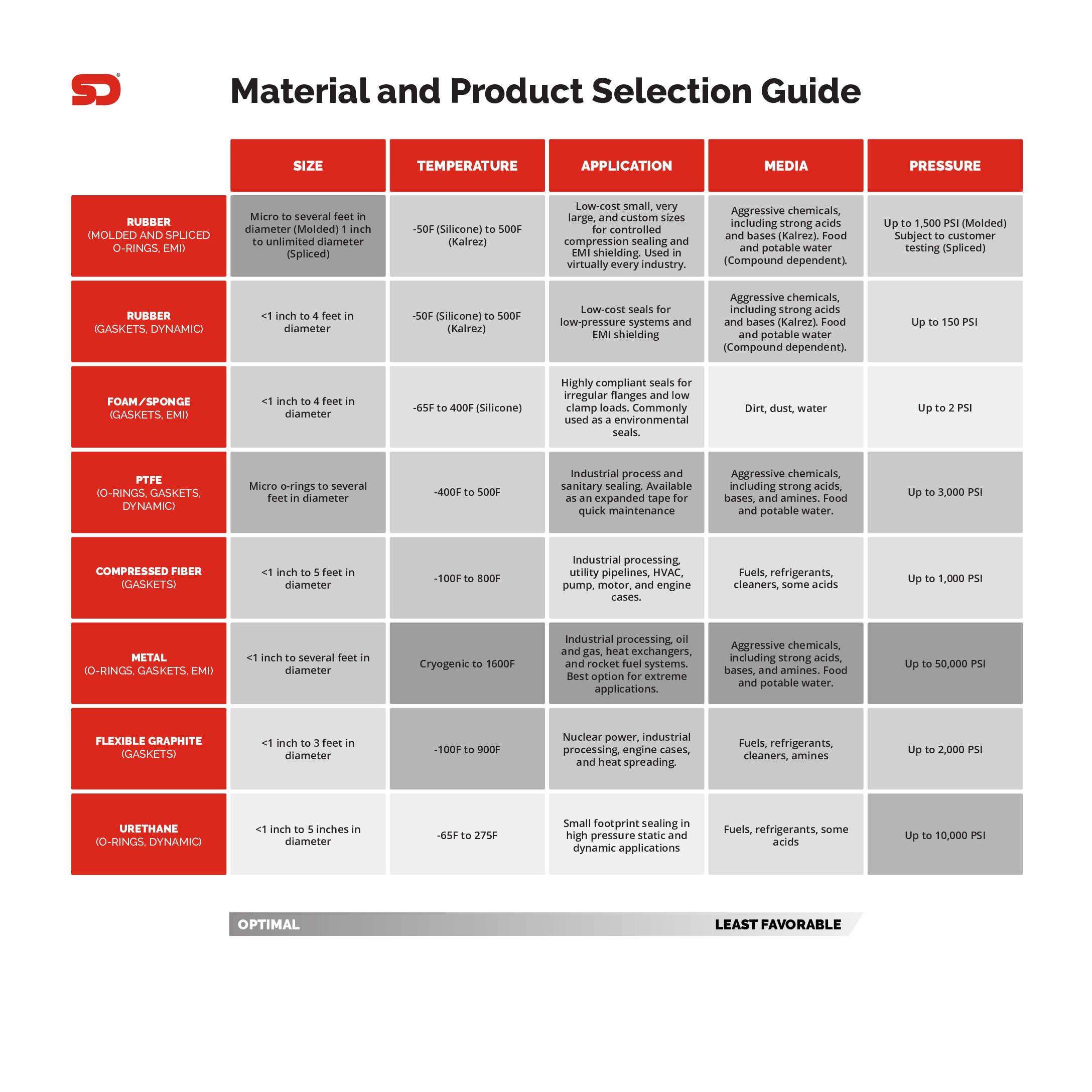
Download Our Material & Product Selection Guide
When you submit the form for the Material and Product Selection Guide, you’ll gain access to a comprehensive chart to assist you in selecting the perfect gasket for your needs. This detailed guide covers various sizes, temperatures, pressures, and more, ensuring you have all the information necessary to make the right decision!
Installation Tips
- Before installing a gasket, be sure that the old gasket has been completely removed and that the flange surface area is clean of debris. You may need to use a metal flange scraper and/or an aerosol gasket remover. It is also recommended that the surface be wire-brushed and inspected for damage.
- Whenever possible, use thinner gaskets. However, flanges that are warped, bowed, or severely pitted require thicket gaskets.
- Whenever possible, use ring gaskets. Full face gaskets have more square inches, requiring additional compressive load on the gasket.
- For anti-seizes, dry is always better than wet. Talc is best, while graphite and mica are also acceptable. Never use metallic-based anti-seize, since particles may accumulate in the surface imperfections, thereby creating a flange surface that is too smooth to be effective.
Proper Gasket Installation
A few simple precautionary measures must be observed in installation to ensure the most satisfactory joint.
- Center the gasket on the flange. This is extremely vital, especially where raised faces are involved.
- Be sure surface finish and flatness are satisfactory.
- Tighten the bolts to compress the gasket uniformly. This means going from side to side around the joint. See Bolting Pattern Below.
- Use a torque wrench, well-lubricated fasteners and hardened flat washers to ensure correct initial loading.
- All bolts should be tightened in one-third increments, according to proper bolting patterns.
- Make a final check pass at the target torque value moving consecutively from bolt to bolt.
- Re-torque 12 to 24 hours after initial installation. All applicable safety standards including lockout/tagout procedures should be observed.
- Never use liquid-based or metallic-based anti-stick or lubricating compounds on the gaskets. Premature failure could occur as a result
Sealing Devices leverages decades of experience in manufacturing and distributing high-performance gaskets, trusted across industries such as aerospace, industrial, electronics, and more.
Whether you need standard or custom gaskets, our team is committed to providing solutions that optimize reliability, efficiency, and performance. Reach out to our applications engineering team for expert advice and support on your next project.