Innovative Thermal Management and Sealing Solutions for Next-Generation Electronics

Key Market Drivers:
- Higher Power Requirements: Advanced electronics require superior thermal management solutions to handle higher power loads
- Higher Computing Speeds: Efficient thermal materials are essential for supporting faster processing speeds
- Smaller Form Factors: Compact designs need creative thermal sealing solutions and thermal gap pads
- Extended Product Life: Durable materials are required to extend the lifespan of products
- Reliability: High-quality solutions are needed for consistent performance and reliability
As these market drivers push the boundaries of electronic device design and functionality, they also introduce a range of new challenges.
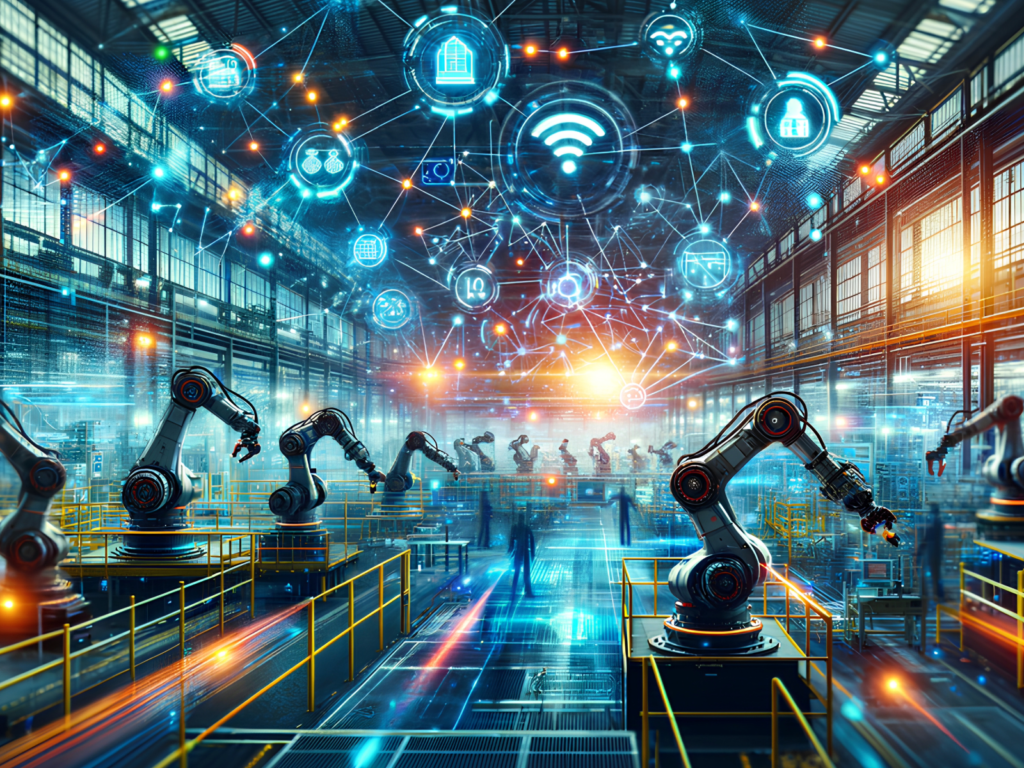
Challenges in High-Power Electronics:
- Overworked Energy Grids: Increasing power use can put a strain on current infrastructure
- Excessive Heat Generation: High-powered components generate substantial heat that needs to be managed effectively
- Pressure on Seals: Elevated temperatures increase the stress on enclosure seals
- High-Frequency Signal Escape: Thermal stress can lead to high-frequency signal escape from devices
- Efficiency Loss: Issues such as heat and pressure can result in decreased efficiency or device failure
Evolving Marketing Trends:
To address these challenges, the market for thermal materials is rapidly expanding. New, key trends include:
- Higher Thermal Conductivity: Advanced materials with thermal conductivity ensure efficient heat dissipation
- Lower Thermal Impedance: Materials designed to reduce thermal resistance, enhancing overall device performance
- Enhanced Compliance and Conformability: Materials that can easily conform to irregular surfaces for better integration
- Reduced Weight: Lightweight solutions for compact and efficient designs
- Regulatory Compliances Adhering to stringent requirements, such as ASTM E595 outgassing standards for material outgassing
Our Solutions:
At Sealing Devices, in collaboration with our suppliers, we offer a range of cutting-edge products designed to meet the rigorous demands of high-power electronics. Some new product offerings from Parker Chomerics include:
Thermal Gels:
Dispensable, one-component gels that conform to irregular surfaces with minimal compression force. Available in silicone and non-silicone formulations with thermal conductivities running from <1 to 7.5 W/m-K.
- Therm-A-Gap Gel 35VT : A reworkable thermal gel designed for vibration and vertical installation, with a typical thermal conductivity of 3.5 W/m-K
- Therm-A-Gap Gel 50VT : A high-tack thermal gel suitable for vibration and vertical installations with a typical thermal conductivity of 5.2 W/m-K.

Thermal Gap Pads:
Customizable sheet materials offering high thermal conductivity. Ideal for filling voids and conforming to heat sink surfaces. Available with thermally conductive pressure-sensitive adhesive.
- Thermal Gap Pad 30 : A soft, low-cost conformable pad with a thermal conductivity of 3.2 W/m-K.
- Thermal Gap Pad 60 : A high-performing pad with low compression force, providing a thermal conductivity of 6.0 W/m-K.
- Thermal Gap Pad 70TP : A soft pad (15 shore 00) with high performance, offering thermal conductivity of 7.0 W/m-K.
- Thermal Gap Pad 80: The highest-performing pad with a thin construction (0.020”) and thermal conductivity of 8.2 W/m-K.
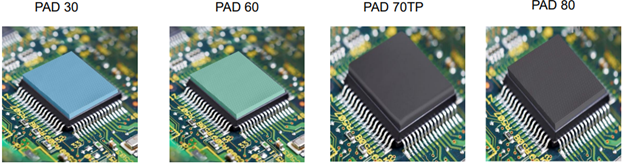
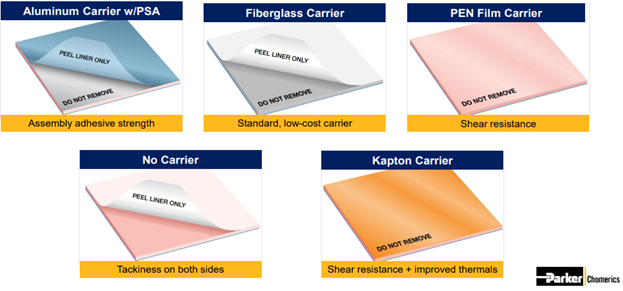

Thermal Potting Compounds:
Two-part dispensable materials that encapsulate and protect high-power electronics. These thermal potting compounds offer robust thermal conductivity and reliability under physical stress, with some compounds meeting ASTM E595 outgassing standards.
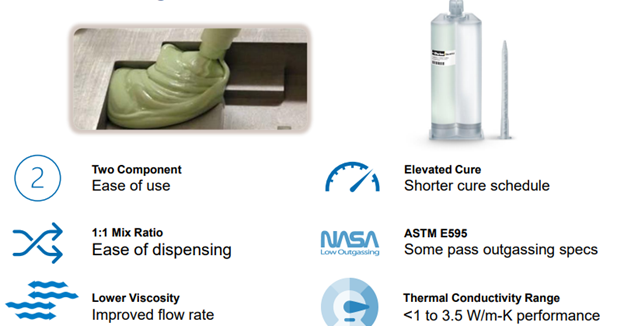
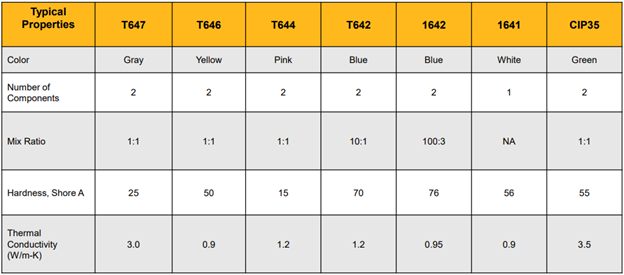
Explore Our Solutions:
Discover how our thermal management solutions and thermal sealing solutions can enhance your high-power, compact technology. Contact us to learn more about our advanced products and how they can support your electrified vehicles and other emerging technologies.