Customer Overview
A leading defense prime contractor, which primarily contracts with the government and military for large-scale defense projects, was developing a sophisticated RF electronics device. This device, using Radio Frequency (RF) technology, is used in communication systems, radar, and other applications requiring the transmission and reception of electromagnetic waves.
The project had several stringent requirements:
- Minor exposure to jet fuel: The device must withstand minor contact with jet fuel, indicating its use in environments such as aircraft or airfields. This necessitates materials and components that are resistant to chemical corrosion and degradation.
- Precise placement of components: Accurate positioning of components on a conductive-coated machined aluminum housing is crucial for the device’s performance. Any misalignment could affect its functionality.
- EMI shielding: The aluminum housing is precisely machined and coated with a conductive material to provide electromagnetic interference (EMI) shielding, protecting the internal components from external electromagnetic fields.
Additionally, the customer needed to produce between 100-200 units of this device each month over a three-year period, indicating a substantial production volume and need for a reliable, repeatable manufacturing process.
Customer Problem
The customer was designing an RF electronic device that required a gasket to provide both EMI shielding and protection against external environmental factors, including minor jet fuel exposure. The gasket needed to be precisely positioned on a conductive-coated machined aluminum housing. The design faced several challenges:
- Irregular Gasket Shape: The gasket’s long unconnected features and small pass-thru holes complicated design and installation.
- Exhausted Gasketing Options: The customer considered adhesive-backed extrusions and conductive sheet gaskets, but these did not meet all requirements.
- Dimensional Constraints: Solutions needed to be wider than the thin-walled raised ribs.
- Thin Inner Walls: The aluminum housing had thin inner walls (0.060 wide) to reduce weight.
- Installation Difficulties: Consistent gasket placement was challenging with the proposed solutions.
Despite exploring various solutions like adhesive-backed extrusions and conductive sheet gaskets, achieving consistent installation and meeting both EMI shielding and environmental protection requirements remained difficult.
Download a PDF version of the case study here
Customer Requirements
•EMI Shielding: The gasket must provide effective electromagnetic interference (EMI) shielding to protect the RF electronic device’s internal components from external electromagnetic fields. This is essential to ensure the device operates reliably in environments with potential EMI sources.
•Precisely Placed Gasket: Accurate and consistent placement of the gasket on the conductive-coated machined aluminum housing is crucial.
•Fuel Exposure Resistance: The gasket must resist minor exposure to jet fuel, indicating the need for materials that can withstand chemical corrosion and degradation.
These detailed requirements emphasize the critical need for a high-performance Form-In-Place gasket solution that addresses both EMI shielding and environmental protection challenges.
Solution Partner
Sealing Devices offers industry-leading products from top suppliers such as Parker, Garlock, Flexitallic, 3M, Gore, Loctite, Rogers, and more. Explore our full list of suppliers here.
How Did Sealing Devices Get Involved?
The customer, already engaged in other projects with Sealing Devices, reached out to request design assistance for this particular challenge. The Applications Engineering team at Sealing Devices reviewed the application requirements and collaborated directly with the customer to develop a tailored solution. They proposed a Form-In-Place (FIP) gasket solution, which involved robotically dispensing the gasket material to ensure precise and consistent placement. This approach addressed the need for both EMI shielding and fuel exposure resistance.
Our Applications Engineers play a crucial role in delivering customized sealing solutions. They bring a deep understanding of materials and applications, working closely with customers to ensure that each solution is perfectly suited to the specific requirements of their projects.
We also specialize in fabrication and converting services for seals, ensuring precise customization to meet your exact specifications. Partnering with Sealing Devices means accessing decades of seal manufacturing and customization expertise.
Sealing Devices’ Solution: Form-In-Place (FIP) Gasket for EMI Shielding and Environmental Protection
The conductive-filled elastomers bonded directly to the housings, leveraging the aluminum housing’s structural integrity. This approach was particularly effective in accommodating the housing’s thin walls, measuring just 0.060 inches wide, without compromising strength or performance. The FIP gasket material could be accurately formed even in small, intricate areas of the housing.
The housings were engineered with compression stops to achieve optimal sealing performance. These stops were strategically placed to compress the gasket material to a precise thickness, typically 25% of its original dimension. This controlled compression not only maximized environmental sealing against external contaminants but also enhanced EMI shielding to protect the device’s sensitive internal components.
Along the perimeter of the housing, a raised outer edge of the gasket served multiple purposes. It provided additional EMI grounding, crucial for maintaining electromagnetic compatibility. Additionally, this raised edge set the compressed gasket height uniformly around the housing, ensuring consistent performance across the device. Moreover, it offered mechanical protection, preventing direct contact that could potentially damage the gasket.
• Controlled Compression: Designed with compression stops, the gasket was uniformly compressed (typically 25%), enhancing both environmental and EMI sealing effectiveness.
• Metal-to-Metal Contact: A raised outer edge around the gasket served multiple functions: providing additional EMI grounding, maintaining consistent compression height, and safeguarding against direct contact.
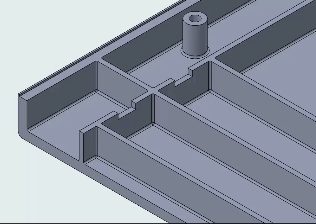