In most military applications, electronic connectors will be standard sizes under the MIL-DTL-38999 specification. It should be noted that many non-military producers will also use these standard connectors, since they are tested in the harsh environments experienced in oil & gas, automotive, and other markets. These connectors will be tested to environmental and EMI tests independently of their end use, and it is up to the end user to design how the connector will be utilized in the final product.
MIL-DTL-38999 connector part numbers contain 6 sections:

- Shell Type
- Material and Finish
- Shell Size
Sealing Devices stocks a number of standard gaskets to meet MIL-DTL-38999, and can quickly cut parts from a variety of materials to meet demand for unstocked items. Parts can be fabricated using traditional die cutting, as well as water-jet or CNC knife cutting. Production methods are determined by quantity, part complexity, and material. Sealing Devices can also manufacture custom connector gaskets outside of the MIL standards, and our team of Application Engineers are available to assist with gasket design for custom connectors.
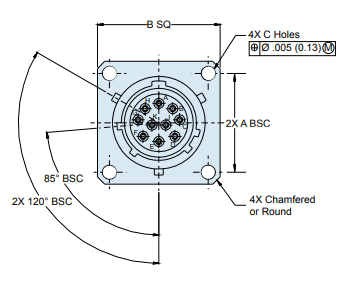
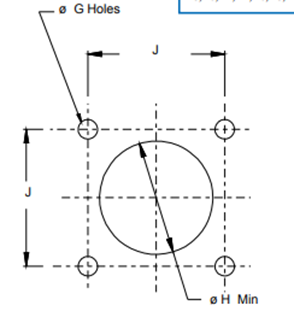
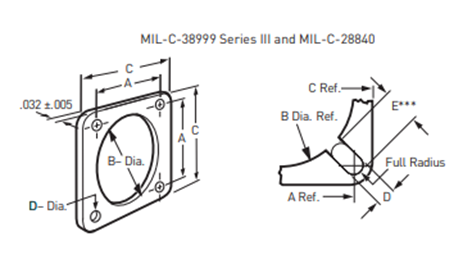
Metal filler options include:
- Nickel – Aluminum
- Silver – Aluminum (MIL-DTL-83528 TYPE B, D)
- Silver – Copper (MIL-DTL-83528 TYPE A, C)
- Nickel – Graphite
- Silver – Glass (MIL-DTL-83528 TYPE M)
Filler selection is dependent on housing material, required shielding effectiveness, what environment the unit will be in, and available budget.
Connectors come in all different shapes and sizes. Whether you have a standard off-the-shelf part number or are designing a new type of connector, Sealing Devices is equipped to supply or help design gaskets for these complex products. Our Application Engineers are ready to assist on your next complex sealing challenge.