High Precision Waterjet Cutting
Perfect for short runs, fast turnarounds, and prototypes
Waterjet cutting is an efficient and cost-effective way to achieve precision cuts of complex and intricate parts using a jet of high-pressure, high-velocity water.
Because no die needs to be created, waterjet cutting is perfect for short runs, prototypes, and custom designs that demand turnaround times as fast as the next day. Waterjet cutting can also be a lower-cost alternative to die-cutting on larger runs of thin materials that can be stacked.
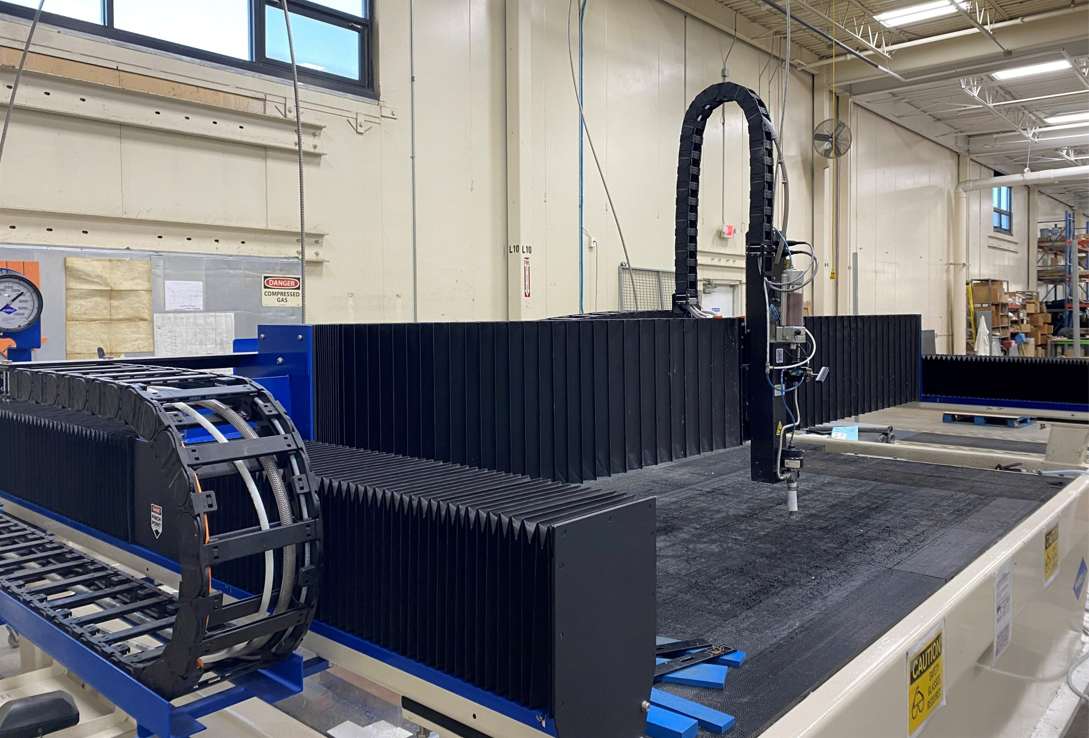
Here’s How It Works:
Once the drawing and specifications are uploaded, the computer calculates the most precise path for the jet. The process uses a high-velocity jet of water that’s pumped through a nozzle at pressures of up to 60,000 psi. Pure water is used to cut softer materials. For higher-density materials, abrasives are added for greater precision. Waterjet cutting is suitable for a variety of materials, including:
- Rubber and sponge
- Foam
- Insulation
- Plastics
- Laminates
- Compressed fiber
- Metal-reinforced elastomer
AN ECO-FRIENDLY SOLUTION
Waterjet cutting doesn’t produce any hazardous waste, so it’s a clean, eco-friendly process. The water that’s used can be recycled through the machine to be reused, and no cooling oils or lubricants are required after cutting.
.
Rely on waterjet for these benefits:
- Ensures structural integrity by eliminating heat distortion and stress
- Eliminates added costs for creating dies
- Results in flawless, precision cuts with tight tolerances
- Provides cost savings on larger runs of thin materials that can be stacked for cutting
- Enables turnaround times as fast as next day
- Offers a cost-effective option for prototype and test parts
- Reduces material waste and improve yield