Chemical processing, petroleum refinement, nuclear power generation, and other heavy industrial processes present unique challenges to ensure safety and efficiency. Aggressive chemical media, high running temperatures and pressures, environmental standards, hefty maintenance costs, and many other factors can all translate to catastrophe if any individual system component fails. Luckily, seal manufacturers have spent decades engineering gaskets to meet and exceed these demands.
PTFE
One solution that’s become indispensable in industrial sealing is PTFE, a durable polymer commonly used as a non-stick coating on cookware. This compound is highly chemically inert, can withstand temperatures up to 500°F (260°C), and readily conforms to irregularities in flange surfaces, making it a reliable and relatively low-cost option for many industrial sealing applications. Specialty compounds can also be formulated for specific performance requirements such as cold flow resistance, fire safety, and FDA compliance. PTFE can also be expanded (ePTFE) to become softer and more conformable, which is valuable when the mating flanges are pitted or somewhat warped. Its low sealing stress also makes ePTFE ideal for brittle glass-lined flanges. PTFE is available as pre-formed gaskets that conform to ASME B16.21 sizing, sheets that can be easily cut to custom geometries, and peel-and-stick tape that has long been used by maintenance technicians in need of a quick seal.
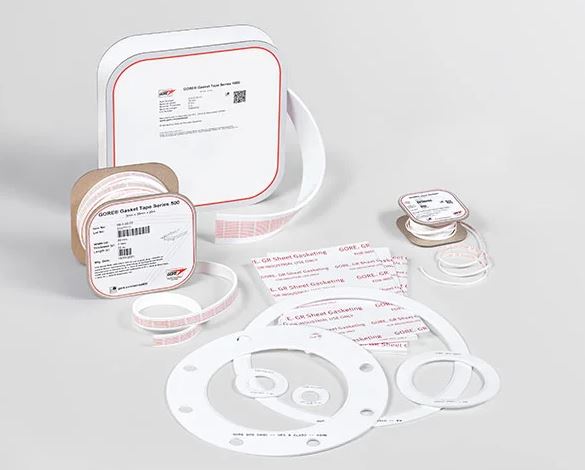
Graphite Foil
For higher-temperature applications, graphite foil is the next step up. Gaskets made from these thin foils are regularly used in nuclear applications since they withstand up to 840°F (450°C) in oxidizing environments. In non-oxidizing environments like nitrogen-blanketed ovens, suitable temperatures can reach up to 5,400°F (3,000°C). Graphite foils can be die-cut to custom or standard sized gaskets, or formed into narrow sealing rings. Foils can also be laminated together to meet specific thickness requirements, or laminated onto stainless steel cores for easier handling and greater blowout resistance. The resulting gaskets are highly compressible and adapt to flange surface irregularities with reduced permeability.
Metallic Gaskets
For applications with the most extreme temperatures, pressures, and chemicals, metallic gaskets such as spiral wounds or kammprofiles are top-of-the-line solutions. These gaskets are designed to ASME B16.20 sizing and accommodate flanges up to Class 2500#, and stand up to temperatures in excess of 1,000°F (540°C). Spiral wound gaskets are made from a thin metal strip wound tightly into a spiral with a non-metallic filler placed between each layer, and can include solid outer and inner rings for increased resistance to blowout and spiral buckling. Kammprofile gaskets consist of a serrated metal core ring with a softer, conformable face material bonded to the sealing surfaces. Gasket performance can be customized with different materials for the winding/core (including stainless steel, nickel, titanium, Inconel, Incoloy, Hastelloy, and Monel), and filler/facing (PTFE, Vermiculite, graphite, and ceramics).
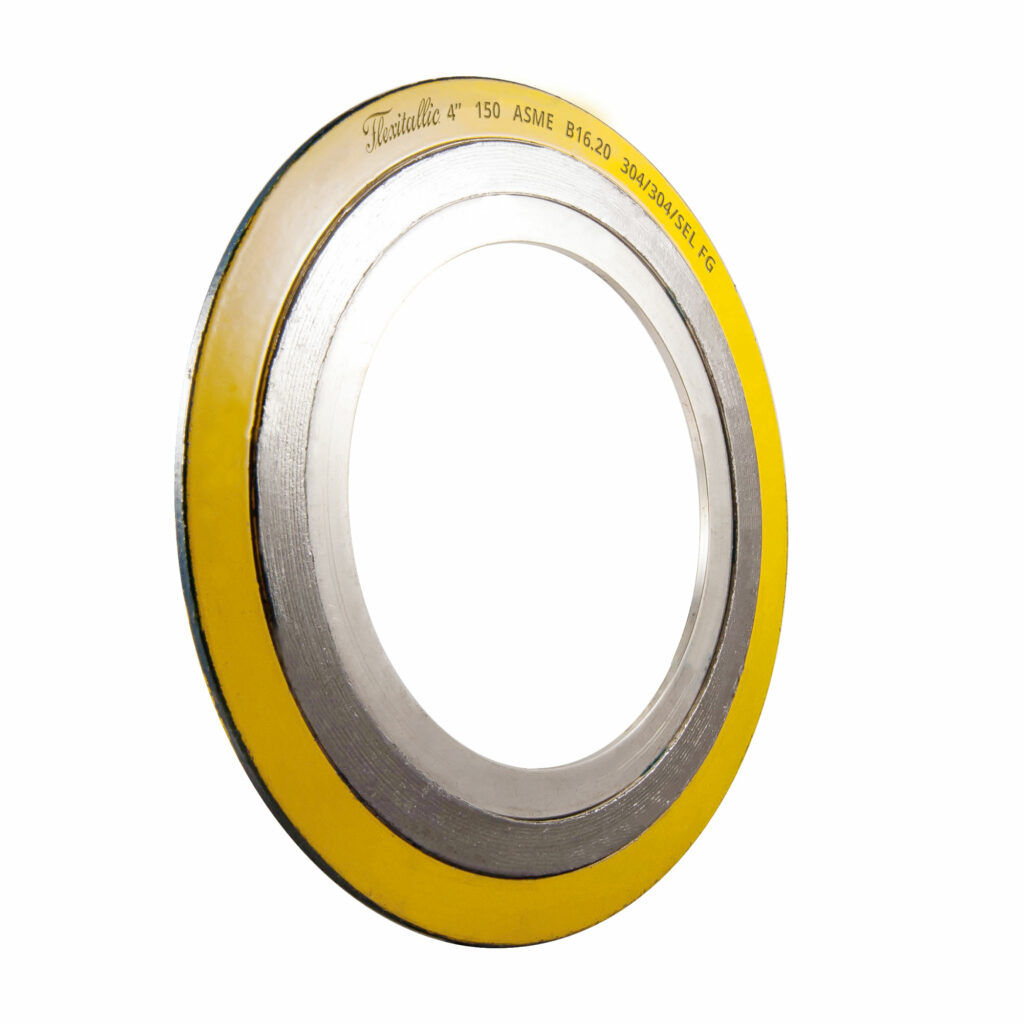
Every sealing application is different, and the materials discussed here are just a few of many available options. Sealing Devices’ engineering, sales, and customer service teams are well equipped to suggest the best gasketing solutions for every industry. Contact us today to find the best fit for your needs.