O-rings are circular sealing devices with a round cross-sectional profile, usually made from rubber compounds (or elastomers). They are simple, easily replaceable, and can be highly economical, which has helped them remain in use for hundreds of years and spread to every industry. When buying o-rings, the 3 most basic characteristics needed are material, hardness, and size. When all of these are defined by a customer, quoting and ordering are as simple as they can be. When any or all of these are not specified, Sealing Devices can make recommendations based on a handful of end-use details, captured by the acronym STAAMPS:
1. Size
As o-rings grew in popularity after their invention, the need to standardize sizing became apparent, leading to the creation of several international standards. The most common standard used in the United States is SAE AS568, which defines over 400 sizes across a range of 5 cross sections. In order to meet demand in an ever-growing number of applications, manufacturers keep molds of many of these sizes readily available to produce thousands of o-rings each day. While the SAE AS568 is the most common, Sealing Devices can supply O-Rings to most international standard sizes. Custom size molded O-Rings can be offered with a one-time tooling charge as well.
Another option, for applications that require non-standard sizes, custom molds may be cut to provide continuous rings in medium and high purchase volumes. Non-standard o-rings can also be fabricated by extruding rubber into a cord and splicing the ends together to meet the required diameter; this option is better for low volumes and can save on tooling costs, especially when the rings can be several feet in diameter. Both cross section and diameter have direct effects on an o-ring’s performance in the conditions below.
2. Temperature
A good seal should both conform to the surfaces which it is sealing against and rebound after being squeezed, and rubber’s elasticity and relative softness have contributed to its status as a leading sealing material. However, when rubber is heated above or cooled below its recommended temperature range it starts to lose its ability to rebound; we call this taking compression set. Most common elastomers are only useful between -40°F and 250°F. However, some silicone compounds are resilient below -100°F, and some FFKM compounds can be used at over 600°F. For even more extreme temperatures, there are metal o-rings that seal up to 1600°F.
3. Application
Many factors of the physical system around the o-ring will affect its ability to seal. The o-ring cross section must be chosen carefully to fit the seal groove: too small of a cross section will not compress enough and allow leaks, while one that’s too large will overfill the groove and start to crack. The diameter of the o-ring depends on the size and style of seal groove: too loose of a diameter will form kinks that can leak, and too tight of a fit can cause the rubber to tear, especially in piston seals and racetrack grooves. The hardness (usually measured as Shore A durometer) will depend on the flange material and finish, as well as the available compressive load; softer materials are preferred for applications with fragile flanges, low fastener load, and somewhat irregular sealing surfaces, while harder materials are better in high-pressure and dynamic applications. When sealing a vacuum, there are even more properties to consider such as permeability and weight loss. O-ring elastomers can also be specially formulated to meet industry-specific standards for aerospace, military, pharmaceutical, food/water, and other use cases, as well as customer-defined requirements such as flame resistance, internal lubrication, and even color.
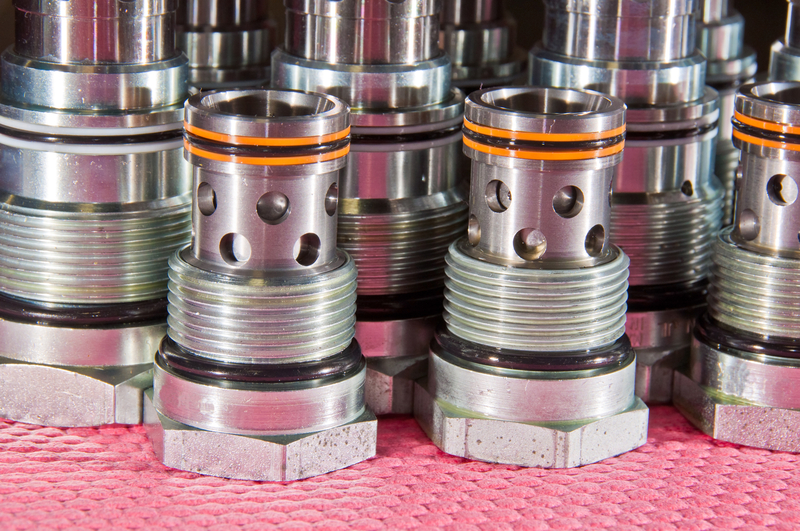
4. Availability
The recent global supply chain complications have revealed just how important and interdependent all stages in the production process are, even for seemingly simple rubber products. While logistical systems are approaching normalcy again, there are still a number of factors affecting raw material availability. Throughout the last couple years, alternative material recommendations have become a common practice to help customers find more readily available solutions without compromising on necessary performance. In certain cases where specific elastomer compounds are not readily available in standard molded ring sizes, o-ring cord can be spliced to fabricate a fitting substitute.
5. Media
When elastomers are placed in contact with chemicals that they are incompatible with, they will swell, degrade, and eventually fail, which can lead to costly and potentially dangerous leaks. Different compounds are resistant to different chemicals, so confirming media compatibility is vital in every sealing application, even with often-overlooked media like steam, ozone, and UV radiation. When necessary, PTFE or metal o-rings can provide more comprehensive chemical compatibility. Parker’s O-Ring and Engineered Seals division has compiled an extensive compatibility table for common elastomers.
6. Pressure
Under normal conditions, rubber o-rings can typically hold up to 1,500 PSI of pressure, but the actual value will depend on cross section, hardware dimensions, and other factors. When the system pressure becomes excessive, the o-ring will start to squeeze through the clearance gap on the unpressurized side of the sealing groove. This action is called extrusion, and if the pressure is not properly regulated the o-ring can start to break apart from this excessive stress. When high pressures are necessary, extrusion risk can be lowered by decreasing the clearance gap, adding an extra anti-extrusion device, or using a harder seal material (including metal in extreme cases that can exceed 50,000 PSI). Back-up rings are common anti-extrusion devices; these are flat rings made of hard rubber or plastic that minimize the clearance gap available for the o-ring to extrude through. On the opposite end of the pressure spectrum, o-ring compounds can also be formulated to seal against a vacuum or rapid decompression (instantaneous loss of pressure).
7. Speed
O-rings can be used to create both static and dynamic seals. In dynamic applications, we tend to use harder o-rings to prevent excessive friction and seal wear. Some elastomers (rubber compounds) perform better than others in sliding and rotating seals, and there are even special formulations of the same elastomers available to further tailor the results. The type of dynamic motion is important too: sliding is more suited to larger cross sections which better resist twisting in the seal groove, but create more friction than smaller cross sections, which is why greater rotational speeds can be achieved with thinner o-rings. Static systems are usually easier to seal, but the details above remain crucial to choosing an o-ring.
As sealing applications become more demanding in all of the areas outlined above, o-ring suppliers have been pushed to continuously innovate seal materials and designs. Given our ties to manufacturers at the leading edge of these innovations, Sealing Devices is positioned as an expert resource to convert all the intricate end-use requirements into a simple sealing solution. Contact us or fill out a technical request form for help with your next sealed design.
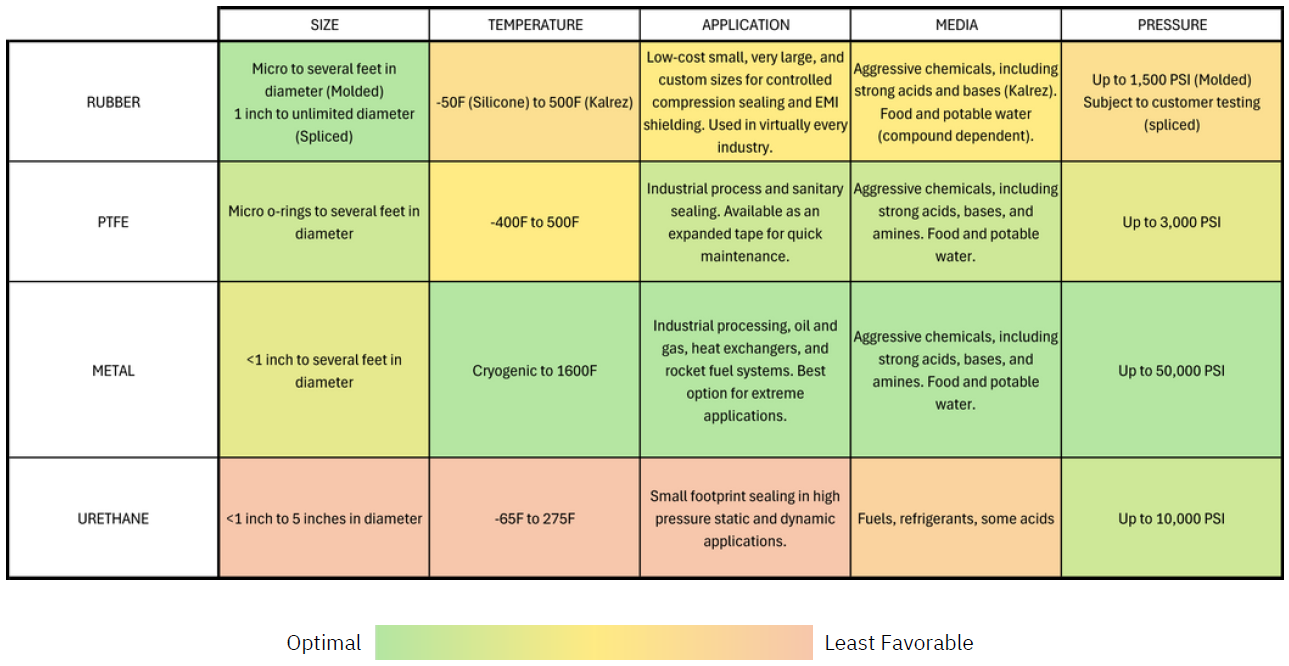